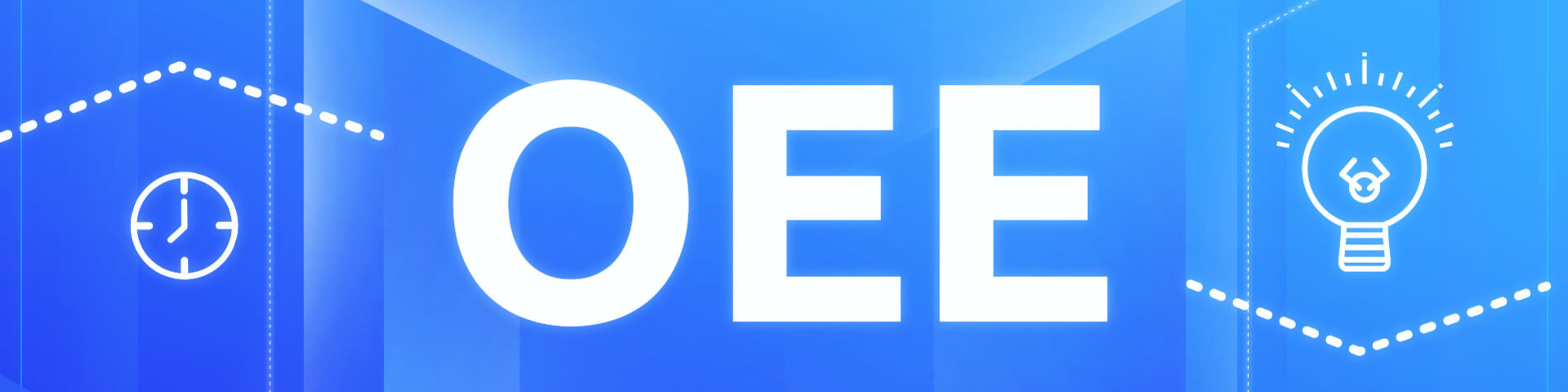
OEE - What does it mean? How to calculate? Examples
OEE - Overall Equipment Effectiveness
OEE - Overall Equipment Effectiveness. It is one of the most important KPIs used in manufacturing to evaluate how effectively a manufacturing process is utilised. OEE is usually expressed in percent and calculated as a product of three other indicators:
- Availability,
- Performance,
- Quality.
Availability
It is the ratio of real working time to the planned working time of the machine or group of machines. In other words, it is the total production time, decreased by any unplanned breaks in reference to the total production time. Planned stoppages, and breaks being a result for example from one-shift work system have no impact on a value of an indicator.
The standards, to which manufacturing plants are striving determine availability typically on 90% level or higher.
Calculations
Example
Data:
- Let us determine previous week’s availability
- Production line worked in three-shift work system from monday to friday
- There was planned(4h) and realised(4h) mechanical inspection
- There was planned(4h) and realised(6h) the oil change
- During the whole week there was one breakdown, which lasted 8h
- During whole week there were 5 changeovers, each lasted 1h
Performance
It is the ratio of number of created products(both good, and broken) to the number of possible number of products to create in work time. Time needed to create single product is named “Standard production time”, calculated by engineers based on their expert knowledge.
The standards, to which manufacturing plants are striving determine performance typically on 95% level or higher.
Calculations
Example
Data:
- All data from the previous example
- During the week, two products, A and B, were being manufactured
- Standard production time for product A is 2.5 minutes
- Standard production time for product B is 2 minutes
- On Monday 500 pieces of product A were manufactured
- On Tuesday 500 pieces of product A were manufactured
- On Wednesday 600 pieces of product B were manufactured
- On Thursday 600 pieces of product B were manufactured
- On Friday 200 pieces of product B were manufactured
Quality
It is the ratio of good (without defects) manufactured products to all manufactured products.
The standards, to which manufacturing plants are striving determine quality typically on 95% level or higher.
Calculations
Example
Data:
- All data from the previous example
- During the week 20 pieces of product A was discarded
- During the week 30 pieces of product B was discarded