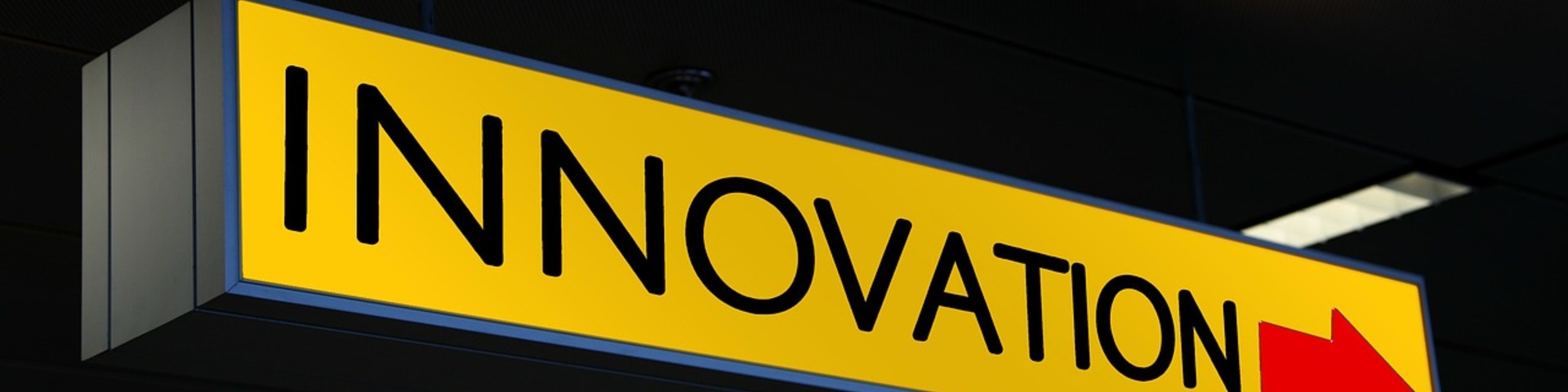
Quick Kaizen as a road to company innovativeness
Kaizen is one of the modern management concepts. In Japanese it means continual improvement of the work performed and refers both to the company management and regular employees. A master and guru of the trend is deemed to be Masaaki Imai, who published a book on the subject in 1986, which immediately gained the status of a bestseller.
Changes introduced in accordance with the Kaizen philosophy occur slowly, but the very process brings measurable results within a longer perspective. For a system based on Kaizen the most characteristic is the emphasis on the process. Such approach requires much effort from the managers in order to improve the particular processes within the organisation. At the same time, thanks to Kaizen, a new work discipline is being developed, better time management, and also team-working skills and capabilities are developed.
Following the assumption of the Kaizen philosophy, the Japanese Toyota achieved an international success with its production system, which has been continuing on a daily basis.
Kaizen at a company
The methodology proposed by Masaaki Imai is to engage all employees in the improvement process. Every employee shall continually analyse the activities performed, control the principles of conduct as well as the methods and standards of the work performed. In that manner errors and irregularities within the company operation may be found and eliminated.
Kaizen actions may be carried out in many different ways.
The first action is a change in the relevant process such as to make it more efficient and safe. Another one is focused on process quality.
Process Kaizen
It is a method applied to draw the employees’ attention to the importance of minor improvements. In that model the employees search for small solutions which may be implemented in the shortest possible time. This works contrary to the classical models of work effectiveness improvement, which usually set out much longer periods between a concept and the final project performance.
Flow Kaizen
It deals with continuous flow of materials and information. Frequently, it is identified with the comprehensive reorganisation of the production area, or even the whole company. Flow Kaizen also means remodelling and improvement of workstations as well as betterment of the methods of performing duties by the employees.
Kaizen implementation
Kaizen is strongly related to another management method also developed in Japan in the 1950s. That is the so called Deming Cycle (also known as PDCA), covering four areas of action considered to be the pillars of the Kaizen philosophy:
- Plan – create an action plan which will make the process performance more efficient;
- Do – execute the plan;
- Check – identify the potential problems and wastage, check all phases of the optimised process;
- Act – or Adjust – implement corrective actions in order to remedy the irregularities found at the preceding stage.
The Deming Cycle should be applied in a continuous manner. It is possible only as a result of a gradual – which means slow – adding of improvements focused on comprehensive optimisation of production processes and reasonable use of the organisation’s resources.
Quick Kaizen – tools supporting the innovation policy
Is it worth to have a continuous improvement department at an organisation? Definitely a better solution is to make the whole company one huge innovation department, every day.
We already know that it is a completely realistic strategy of development of any company, enabling the engagement of the employees to report improvement ideas. For that purpose tools such as Quick Kaizen are applied, which will prove to be effective where there is a need for simple changes.
For that purpose interactive problem management systems may be used, as well as gradual knowledge base created and new ideas generated.
In that way, the company gains high quality information exchange among the employees of various levels. Training processes accelerate and creativity is raised among the employees, which is further translated into fast problem solving.
It is, therefore, worth rejecting the hardly effective methods of creativity management, lists of ideas in Excel type spreadsheets or paper forms. Using the web and mobile engineering solutions, the exchange of information regarding key process elements may be accelerated by following it online, which includes:
- reporting the perceived problems,
- proposing new solutions (innovativeness ranking),
- promoting good practices (reward catalogue),
- documenting the particular process events,
- recording information crucial for further development,
- building a solid knowledge base,
- rewarding good ideas through a bonus system,
- improving information flow.
Thanks to that every employee engaged in the changes may follow the problems reported by others and perceive their potential solutions.
Summary
Kaizen, as a tool of “small steps”, systematically and gradually leads to changes which are to ensure long-term effect within a specific time horizon. The results are rarely visible at once, but when every employee has introduced a dozen or more seemingly minor improvements a year, the effect is marked and perceptible.
For a majority of western companies and organisation, a methodology based on the Kaizen philosophy means first of all a change of the whole corporate culture. This is a key to success.