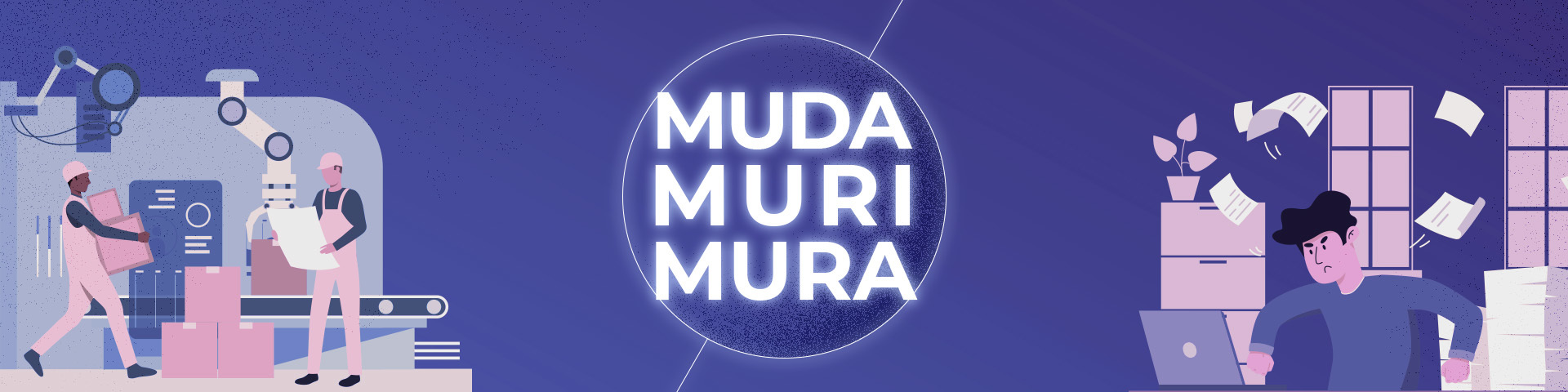
Czy w Twojej fabryce panuje Muda?
Nie chodzi o brak zajęć czy zniechęcenie wśród załogi. Tematem artykułu jest Muda co z języka japońskiego można tłumaczyć jako straty lub marnotrawstwo. Muda jest jednym z trzech, obok Mura (nieregularność) i Muri (nadmierne obciążenie pracą), głównych przyczyn niskiej efektywności działań w zakładzie produkcyjnym.
Czym jest Muda?
Jak większość terminów i pojęć związanych z lean management, również Muda pochodzi z kraju kwitnącej wiśni, a służy określeniu czynności i zjawisk, które zużywają zasoby, lecz nie tworzą wartości dla klienta.
Główne obszary strat
Analiza efektywności produkcji pozwala określić 7 lub 8 głównych obszarów strat. Niektórzy bowiem jako ósmy czynnik wymieniają “niewykorzystany potencjał pracowników”. Celem łatwiejszego zapamiętania nazw obszarów, stosowany jest termin TIM WOOD będący akronimem angielskich słów: Transportation, Inventory, Motion, Waiting, Overproduction, Overprocessing, Defects.
Zbędny transport (ang. waste of transportation)
Niepotrzebne przemieszczanie produktów lub materiałów generujące straty czasowe, finansowe oraz powodujące dezorganizację. Zbędny transport może mieć miejsce zarówno w obrębie organizacji, jak i pomiędzy firmami. Wybitnie kosztowym przejawem tego typu straty są tzw. taksówki, czyli konieczność wysyłania brakującej partii produkcyjnej osobnym transportem, głównie z powodu opóźnionej produkcji.
Nadmierne zapasy (ang. waste of inventory)
Większa niż zakładane minimum i przewyższająca zapotrzebowanie w jednostce czasu ilość surowców i półproduktów. Nadmierne zapasy mają negatywne skutki finansowe ze względu na zamrażanie środków finansowych, a także konieczność utrzymywania dużych przestrzeni magazynowych. Przechowywane surowce i półprodukty mogą stracić swoją jakość i przydatność do wykorzystania w procesie produkcyjnym co również niesie za sobą negatywne konsekwencje dla finansów organizacji.
Zbędny ruch (ang. waste of motion)
O ile w powyższych aspektach chodziło zwłaszcza o niedoskonałość procesu, to w przypadku “zbędnego ruchu” problem tkwi w niewłaściwej ergonomii stanowiska pracy lub braku odpowiedniego instruktażu stanowiskowego pracownika. Skutkuje to zbędnym wysiłkiem fizycznym wykonywany przez pracownika w trakcie wykonywania pracy, np: chodzenie, sięganie po przedmioty, schylanie się, przechodzenie z miejsca na miejsce.
Oczekiwanie (ang. waste of waiting)
Wszelakie oczekiwanie na komponenty czy półprodukty, a także bezczynne czekanie na zakończenie procesu, np. operację na maszynie skutkuje marnotrawstwem czasu pracy pracownika i/lub maszyny. Dobrym przykładem obrazującym problem i jego rozwiązanie jest porównanie efektywności pracy na prasach jednostronnych i dwustronnych.
Na prasach jednostronnych operator układa elementy w zadanej konfiguracji, a maszyna czeka na zakończenie tego działania. Następnie prasa wykonuje swoje zaprogramowanie działanie, a czeka operator. Efektywnie stanowisko pracy działa przez około 50% czasu, a połowę czasu jest bezczynne. Na prasach dwustronnych znajdują się 2 miejsca, w których operator układa elementy. Podczas kiedy elementy są układane, drugi zestaw jest obrabiany przez maszynę. Następnie operator przechodzi na drugie stanowisko, demontuje produkt, układa komponenty na II zestaw, a prasa na pierwszym stanowisku wykonuje swoje działanie. Cykl się zamyka, a marnotrawstwo może być zredukowane nawet do 0 w przypadku, kiedy czas układania elementów przez operatora jest równy z czasem wykonania operacji przez prasę.
Problem oczekiwania może mieć także tło nieprodukcyjne, np. może być spowodowany oczekiwaniem na akceptację, podpis, zezwolenie czy decyzję administracyjną.
Nadprodukcja (ang. waste of overproduction)
Wytwarzanie produktów, których wolumen przewyższa zapotrzebowanie. Czasami jest to wynik niewłaściwej organizacji i słabej komunikacji. Zdarzają się jednak przypadki, kiedy jest to celowe działanie mające na celu zawyżenie wskaźnika performance’u. Produkowanie w nadmiarze jest niezgodne z metodą just-in-time, która była i jest charakterystyczna dla systemu produkcyjnego Toyoty.
Nadmierne przetwarzanie (ang. waste of overprocessing)
Każda czynność, która nie jest niezbędna do wytworzenia produktu lub usługi o wymaganych przez klienta parametrach i poziomie jakości. Może to być: nadmierne raportowanie, zastosowanie zaawansowanych i drogich technologii oraz maszyn, ale także zbędne podróże służbowe, nadmierne i uciążliwe kontrole lub niepotrzebnie zwoływane zebrania.
Błędy i wady jakościowe (ang. waste of defects)
Wadliwe produkty powodują bezpośrednią stratę. Nawet jeśli z produktu wadliwego został odzyskany inny wartościowy produkt to strata jest znacząca i wynika nie tylko z niższej wartości odzyskanego produktu, ale także z konieczności poświęcenia dodatkowych zasobów na tą operację.
Nazbyt liczne wady powodują także konieczność wdrożenia dodatkowych kontroli, bardziej wnikliwych selekcji i wieloetapowych procedur akceptacji, gdyż każda wadliwa część, która trafia do klienta zewnętrznego powoduje zarówno straty finansowe (dodatkowe wysyłki, kary umowne, itp.), ale również wizerunkowe.
Niewykorzystany potencjał pracowników (ang. waste of untapped human potential)
Niewykorzystywanie przez organizację pomysłów, kompetencji, szczególnych umiejętności pracowników, a także przydzielanie im zadań spoza lub poniżej ich kompetencji. Jest to także niewykorzystanie pomysłów, które mogą pojawić się na każdym szczeblu w hierarchii organizacji, a których kierownictwo działające na wyższym poziomie ogólności, zwykle nie zauważa. Do tej grupy należy niezliczona grupa porzuconych pomysłów dotyczących ergonomii stanowiska pracy czy optymalizacji procesów jednostkowych.
Podsumowanie
Straty i marnotrawstwo zawsze będą obecne w każdej organizacji produkcyjnej. Zadaniem managementu jest jak największe ich ograniczenie, głównie poprzez zwiększanie świadomości uczestników procesu produkcyjnego na każdym szczeblu. Żadne działania nie odniosą tak dobrego skutku jak zwiększenie kultury korporacyjnej i poczucia odpowiedzialności jednostki za dobrze wykonane działanie.
Marnotrawstwem i stratą byłoby jednak nie wspomnieć o narzędziach, które wspierają wysiłki kierowników i pominąć fakt, że jako firma z wieloletnim doświadczeniem specjalizująca się w oprogramowaniu dla zakładów produkcyjnych, odnieśliśmy wspólnie z naszymi klientami wiele spektakularnych i trwałych sukcesów.
Oto lista wdrożonych rozwiązań, które w sposób znaczący przyczyniły się zniwelowaniu negatywnych skutków mudy w obszarach produkcji, logistyki, utrzymania ruchu i transportu.
eKANBAN
Elektroniczny KANBAN to aplikacja znacząco poprawiająca transport na hali produkcyjnej. Wpływ aplikacji na muda to głównie:
- eliminacja zbędnych transportów
- eliminacja nadmiernych zapasów
- redukcja opóźnień dostaw
Action Plan
Kompleksowe narzędzie do zarządzania organizacją o strukturze piramidalnej, wyposażone w specjalizowane moduły do prowadzenia audytów, realizowania zmian inżynieryjnych i oceny pomysłów pracowniczych. Wpływ aplikacji na muda to głównie:
- wykorzystanie potencjału pracowników m.in. dzięki zautomatyzowanemu procesowi oceny i wdrażanie pomysłów pracowniczych, tzw. Quick Kaizen
- redukcja oczekiwania dzięki natychmiastowej propagacji informacji w całej strukturze organizacyjnej
ePlanning
Jest to grupa dedykowanych rozwiązań, wdrożonych w sposób indywidualny u wielu klientów, zwiększających przejrzystość działań związanych z planowaniem i rozliczaniem produkcji. Oprogramowanie to jest wyposażone w elementy business intelligence pozwalające na generowanie raportów i monitorowanie podstawowych wskaźników efektywności produkcji, takich jak: OEE, MTTR, MTBF, Quality, Availability czy Plan vs Real.
Wpływ aplikacji na muda to głównie:
- redukcja oczekiwania poprzez monitorowanie efektywności pracy operatorów
- zmniejszenie ilości defektów, poprzez obserwację ich ilości i przyczyn
- eliminacja nadprodukcji dzięki przejrzystemu modułowi planowania oraz raportom przedstawiającym performance tylko w kontekście złożonych zamówień
Wyżej wymienione przykłady stanowią jedynie część działań, którymi zajmuje się Ruby Logic współpracując z zakładami produkcyjnymi z całej Europy. Gorąco zachęcamy do kontaktu zarówno w temacie wdrożeń jak i możliwej współpracy oraz wymiany kompetencji.