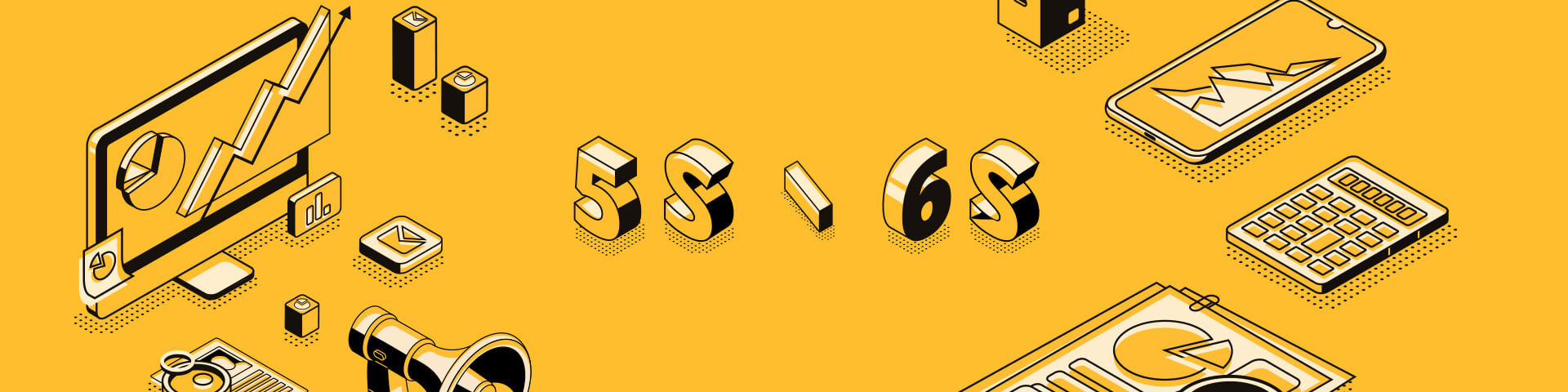
System 5S - narzędzie, bez którego nie sposób wyobrazić sobie współczesnego zarządzania
“Wszystko ma swoje miejsce i wszystko na swoim miejscu” - to hasło obrazuje główne założenia metodologii organizacji pracy 5S, której nazwa pochodzi od japońskich słów: Seiri, Seiton, Seiso, Seiketsu, Shitsuke. Można je przetłumaczyć jako: selekcja, systematyka, sprzątanie, standaryzacja, samodyscyplina. Czym jest tajemniczy skrót 5S i w jaki sposób wdrażać go w firmach, aby w pełni spełniał swoją rolę i pomagał im w procesie zarządzania produkcją?
5S jako element Lean Management
System 5S to jedno z najważniejszych narzędzi wchodzących w skład metodyki Lean Management, która swoje początki miała w branży wytwórczej. Na początku ograniczała się jedynie do modelu zwanego Toyota Production System (TPS), jednak z czasem ewoluowała do czego znacznie większego. Głównym założeniem modelu było zredukowanie strat występujących w procesie produkcyjnym.
Cała koncepcja Lean Management opiera się na założeniach:
- Elastyczności struktur organizacyjnych * Ciągłym doskonaleniu kadry (poprzez kursy i szkolenia) * Wyodrębnieniu mniejszych zespołów, pracujących nad określonym zadaniem * Podziale odpowiedzialności
Głównym celem Lean Management jest minimalizowanie zapasów, maksymalizowanie zdolności produkcyjnych, tworzenie maksymalnie krótkich cykli produkcyjnych, terminowość dostaw oraz partnerska współpraca z dostawcami
Kroki w systemie 5S
5S to pięć ściśle określonych kolejnością punktów, które powinny być realizowane na stanowiskach pracy. Ważne jest, aby nie zmieniać ich kolejności oraz skupić się na dokładnym wykonaniu każdego z punktów.
1. Sortowanie
Sortowanie - oddzielenie ważnych i mało istotnych elementów na miejscu pracy - instrukcji, narzędzi, itd. Niepotrzebne elementy należy wyrzucić lub odpowiednio oznaczyć czerwoną etykietą. Celem jest utrzymanie czystości na miejscu pracy poprzez wyeliminowanie niepotrzebnych elementów, które mogą zaburzać pracę.
2. Systematyka
Systematyka to dalsza praca nad organizacją stanowiska. Składa się m.in z wyznaczenia stref ważnych i mniej ważnych elementów pracy. Warto wykorzystać tutaj kolory, aby łatwiej było oddzielić miejsca istotne. Ważne jest także wyznaczenie kierunków oraz limitów ilości na stanowisku, np. materiałów.
3. Sprzątanie
Jak sama nazwa wskazuje punkt związany jest z utrzymaniem czystości na stanowisku pracy. Co jednak ważne, nie chodzi jedynie o wyczyszczenie narzędzi. Głównym celem sprzątania jest przegląd narzędzi w celu wykrycia ewentualnych nieprawidłowości. Warto w tym miejscu określić schemat i harmonogram sprzątania.
4. Standaryzacja
Ustalenie harmonogramów audytów, dzięki którym system 5S jest w stanie dobrze funkcjonować, a także systematykę poruszania się po stanowisku pracy. Chodzi tu przede wszystkim o to, aby stanowisko było odpowiednio opisane - każda osoba, która znajdzie się na nim, musi dokładnie wiedzieć, w jaki sposób się po nim poruszać.
5. Samodyscyplina
Ciągłe doskonalenie, realizowanie zadań wynikających z audytów. Ważne jest, aby pracownicy nie traktowali audytów jako największe zło. Każdy audyt ma na celu ulepszenie i ewentualne poprawy niedoskonałości. Pracownicy powinny więc dążyć do samodoskonalenia.
6S jako rozszerzenie założeń 5S
Z czasem zauważono jak bardzo wymierne korzyści płyną z zastosowania systemu 5S i zaczął on ewoluować. Tak powstał kolejny, szósty już punkt w metodyce. Chociaż pozostałe punkty powinny być realizowane po sobie (nie można rozpocząć np. od kroku 4), to ostatni, szósty punkt powinno się realizować nadrzędnie. Dlaczego? Ponieważ dotyczy on bezpieczeństwa. Często więc określa się go jako najważniejszy element.
6. Safety (Bezpieczeństwo)
Bezpieczeństwo, do którego zaliczamy szkolenia BHP, środki ochrony osobistej, tablice z ostrzeżeniami na stanowiskach pracy i co najważniejsze - eliminację potencjalnych zagrożeń.
TWI w bezpieczeństwie pracy
Warto w tym miejscu wspomnieć o metodzie TWI (Training Within Industry), która powstała już podczas II Wojny Światowej. TWI jest istotnym narzędziem Lean Management, ponieważ związana jest z ciągłym doskonaleniem oraz poprawą ergonomii stanowiska pracy.
- Instruowanie pracowników
- Doskonalenie metod pracy
- Relacje z pracownikami
- Bezpieczeństwo pracy
Element tej metodyki, który warto wykorzystać w 6S jest Bezpieczeństwo Pracy (BP) czyli skupienie się na zagrożeniach zanim dojdzie do wypadku.
Kroki w TWI BP:
- Identyfikacja miejsc potencjalnego zagrożenia
- Określenie sposobów zaradczych
- Wprowadzenie w życie działań zaradczych (tu także należy pamiętać o szkoleniach)
- Kontrola rezultatów
Checklista
Wartym uwagi narzędziem przy przeprowadzaniu audytów są checklisty z najważniejszymi pytaniami dla każdej z części przedstawionej metodologii. Przykładowa checklista jest dostępna do pobrania w formatach: PDF i XLSX.
Podsumowanie
System 5S/6S może być świetnym drogowskazem, skierowanym na poprawę ergonomii pracy, wzrost efektywności oraz minimalizację wypadków na stanowiskach pracy. Poprawnie wdrożony, poparty instrukcjami i odpowiednimi szkoleniami pracowniczymi, może pomóc liderom w sprawnym zarządzaniu i tym samym przyczynić się do poprawy wyników firmy.