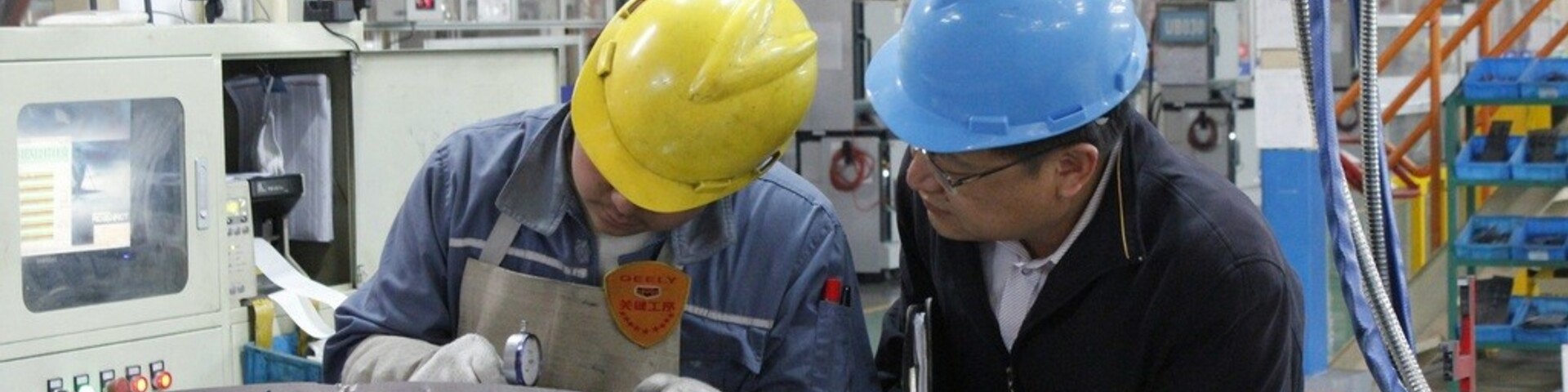
Layered Process Audit – a modern tool to manage quality at a company
Layered Process Audits (LPAs) represent a significant element of improving the quality management system at a company. Effective organisation management, apart from planning and monitoring of the particular processes, requires accurate and effective verification of sources or the occurring non-compliances and implementing adequate remedial actions. The characteristic feature of an LPA is that employees at all levels of the company hierarchy are responsible for carrying out audits.
What exactly do layered audits mean and why are they implemented by the most profitable companies in the world?
What are layered process audits?
Internal audit (including 5S, LPA or TPM) is a set of simple and effective methods which contribute to establishing and maintaining high production quality. It is related to verification of compliance of the operating standards, staff competence and operation of the company as a whole.
LPAs have been developed for checking the compliance of a production processes with the standards and strictly determined specifications, as well as implementation of changes or corrective actions in case of detecting non-compliance. They are mainly applied in controlling manufacturing processes in many sectors around the world. Outside of industry, they are applied less frequently.
Layered audits also comprise the following activities:
- determination of audit levels and their schedules,
- identification of all high-risk elements,
- checklist supporting the assessment of the current processes in compliance with the standards binding at an organisation,
- determination of remedial and corrective measures,
- systematic reviews of the audit results by the authorised persons.
Everyone is an auditor
Unlike in other types of audits, LPAs are not carried out by specialists of only one group.
Nearly everyone, regardless of their place in the organisation’s hierarchy, becomes an auditor. A production operator fulfils the same functions within an LPA as the plant manager. Thanks to that, every employee of the company is aware of the level of quality of the products manufactured. Yet, it must be remembered that the frequency of carrying audits by production staff is definitely higher than in the case of a Management Board member or even a Department Manager.
The first LPA layer is checking the quality of semi- products and correctness of the whole process by a production employee. At another step a supervisor verifies the key process stages and forwards feedback on the process compliance. If needed, remedial actions are introduced.
Identical control is carried out by the employees of further levels within the hierarchy of an organisation management. In that way everyone is an auditor within the meaning of the layered process audits.
Corrective and remedial actions
Identically as in the case of classical quality audits, within an LPA a plan of reaction to the non-compliance detected must be determined and prepared. Non-compliance must be properly documented and documents must generally accessible as a direct point of reference for further audits.
Any non-compliance detected during an LPA must be remedied within a strictly determined remedial or corrective actions. The actions planned for easily foreseeable non-compliance are sometimes prepared even before the planned audit and are based on prior experience of the organisation.
Advantages for the company
The main advantages of implementing LPAs include but are not limited to:
- more effective standardisation of processes within an organisation,
- updating of the particular process stages,
- higher safety level on workstations
- ensuring interaction between the managers and production operators,
- direct feedback from the operators ensuring the possibility of immediate implementation of corrective actions,
- errors elimination,
- reduction of the quantity of waste,
- product quality improvement,
- higher customer satisfaction.
LPA applications
A layered audit is a very effective tool in the process of quality, productivity and safety improvement. Therefore, it has been broadly applied at production plants, particularly at the automotive sector. Layered audit implementation is required, for example, at the suppliers of such international giants as Chrysler General Motors.
LPAs are perfect to be applied both at corporations and at small family companies. Successful implementation guarantees a significant reduction of the number of complaints by effectively preventing of identical problems recurring in the future. It also enables quick identification of areas requiring improvement, and detecting points which generate production waste.
In LPA implementation it is of key importance to fully engage the employees at various levels of the organisation. Thanks to that, the achievement of the TQM principles is more effective. Layered audit may also be a perfect tool to improve the processes of the integrated safety, quality and environmental systems. It may also act as a signpost towards the improvement of production effectiveness, ergonomics of manufacturing processes but also minimising the number of errors.
A properly carried out layered audit, preceded by employee instruction and training, is a perfect tool for efficient management, which indirectly contributes to the improvement of results of the whole company.